What is ConiForme?
As a wood-based product capable of acting as a mechanical reinforcer for thermoplastic polymers, ConiForme dramatically improves the targeted properties of a plastic.
It is a bio-sourced and renewable mechanical reinforcer that is compatible with an industrial processes; has proven performance and excellent environmental credentials.
ConiForme can replace glass fibre for short fibre applications. Compared to agricultural fibres, ConiForme is an ideal solution from an industrial perspective. Non-seasonal, it has efficient supply chain management and is user friendly, due to the effective dosing of the fibre-rich dice.
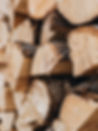
Producing ConiForme
ConiForme can be manufactured in a world-class Medium Density Fiberboard (MDF) plant by modifying the chemistry and adding dicing equipment at the end of the process.
There are 6 major steps to manufacturing:
Step 6
Step 5
Step 4
Step 3
Step 2
Step 1
Wood Chipping
Input wood material used in the process is reduced in size to a square particle (chip) of approximately 25mm and 5 mm thick.
Chip Washing
After screening, wood chips are washed. This is a required step in order to remove bark, soil, sand and abrasive contaminants. This is necessary to protect the refiner discs but it is also a guarantee of the quality of the product sold to our customers. ConiForme is a product free of any contaminants.
Refining
After being heated to 175-190 C with saturated steam, the refiner converts chips into individual fibres. Wood chips are fed into a gap between 2 counter rotating discs. The surface of the discs have a series of raised bars. At the center of the disc, where the chips are introduced, the breaker bar pattern is coarse and at the periphery, the bars are much finer. Consequently, as the wood is driven across the radius of the disc by centrifugal forces, it is broken down into its constituent fibres.
Blending with Additives
The fibres are discharged from the refiner down to a pressurized blowline. Blending of the fibre with additives in the blowline under high pressure facilitates a uniform distribution due to the steam expansion, which causes highly turbulent flow, and rapid accelerations (that separate fibres) to a high velocity of up to 100 m/s.
Mat Forming & Hot Processing
The fibre is then dried and pneumatically conveyed to mat formers. The mat formers are designated to distribute an even layer of fibres onto a continuously moving belt. The hot pressing process applies a combination of heat and pressure to consolidate the mat and convert it to a panel. At this stage, the moisture in the product is constant between 5-8%
Cut to Size & Dicing
After being cut to size for feeding into a pelletizer, the ConiForme panels are reduced to consistent-sized cubes with minimal waste. This is similar to the plastics industry where plastic material is reduced to consistent-sized dice for feed hoppers.


Product
The power of ConiForme and its product potential is in its versatility and customisable nature.
Through selection of polymer grade for reinforcement by ConiForme, final composite properties can be modified to meet target product requirements. Additives such as impact modifiers, nucleating agents or dyes have been successfully used in compound formulation.
Physical attributes improved by addition of ConiForme include: stiffness, strength, thermal dimensional stability, heat deflection temperature, scratch resistance, reduced shrinkage in tooling, and others.
For further information about the design capabilities of ConiForme contact info@conniforme.com The option of Standard and Fast has been developed for the differing capabilities of your industrial equipment. We understand that moisture content is something some of our customers like to control themselves, whereas, others prefer us to supply the right percentage to ensure maximum quality.
Compounding ConiForme
ConiForme is designed to be the most user-friendly alternative in the compounding industry for natural fibre composites. The ConiForme dice are very easy to dose during the extrusion process. ConiForme is used with standard dosing equipment and does not require any chopping or special preparation. Recommendations to maximize the productivity of the compounding lines have been developed:
1
2
3
Before processing:
ConiForme dice have an average moisture content of 5 to 8% by weight when stored under "normal" low humidity conditions. Depending on extrusion conditions and type of equipment (vents, etc.), pre-drying might be critical to obtain a good compound. However, with proper venting during extrusion (both atmospheric and vacuum venting), the standard product 5-8% moisture content has been successfully compounded in many manufacturing sites. Dried wood fibres are hygroscopic, meaning the fibres will readily absorb moisture from air. It is therefore essential to keep ConiForme in a proper low humidity storage area.
Feeding into the extruder:
ConiForme is made of condensed, free-flowing dice, which overcome the feeding issues usually associated with natural fibres (low bulk density). ConiForme is more resistant to bridging or funnel-flow/plugging issues.
Feeding ConiForme downstream, using a side feeder port, into the molten polymer is recommended (especially with higher melting point thermoplastics) to shorten the wood fibre residence time in the extruder and limit the wood fibre thermal degradation. The advantage of this configuration is that the polymer can be aggressively melted, using mixing elements and higher temperatures. While in contrast, after the fibre is introduced, the fibre and the polymer are mixed together using mild dispersive elements and a lower temperature.
A side feeder with a stirred hopper has been successfully used to feed the wood fibre dice into an extruder.
Loss in weight feeder systems can be used and would ensure better control of the dice feeding rate.
Extrusion conditions of CONIFORME:
A key attribute of ConiForme is that it does not require severe mixing extrusion conditions (shear forces/rate) to fully release the dice into individual fibres. As a result of gentler extrusion, fibre length is preserved. A short residence of the wood fibre dice and a melt temperature below 200ºC are essential to avoid thermal degradation of the wood fibres. ConiForme patented recipe was engineered to ensure proper release into individual fibres with a superior aspect ratio.
For a successful extrusion:
1. Use a co-rotating twin screw extruder
2. Keep temperature below 200°C or 390°F
3. Side feed the ConiForme dice
4. Vents with both vacuum and atmospheric
5. Add a coupling agent
6. Design screw with medium dispersion discs, 1/3 mixing - 2/3 conveying
7. Use a co-polymer with MFI greater or equal to 35
Our Advantages
Easy to use - The ConiForme dice are easy to dose during the extrusion process
Renewable and Sustainable - We are committed to making sure that our wood suppliers adopt a Sustainable Forest Management (SFM)
Low Carbon Footprint - The ConiForme production process consumes far less energy than that of glass fibre production
Reduced Equipment Wear - Using wood fibre is significantly softer on tools, screws and barrels, hot runners, and grinders (recycling).
Health & Safety Profile - Our production process removes dust created from processing wood. Using ConiForme minimises fire and dust explosion risks for your business and your staff.

Great Performance
Great Mechanicals
Weight Saving
Scratch Resistance
Colour and Design Cost Competitive
Sustainable Economics
Eco-Friendly
Renewable
Sustainable
Low Carbon Footprint Recyclability
End-of-life
Great LCA
Contact Us
ConiForme is eager to learn about your needs and priorities when it comes to the polymer reinforcement of Polyolefin compounds. We invite you to partner with our team to maximize the results and efficiency of your products and processes.
This new-patented technology offers many advantages including both weight and cost savings with design opportunities unrivalled in the natural fibre sector. Woodforce is neither a by-product nor a residue, it is an industrially engineered wood based product that offers Natural Strength for Plastics.